Les systèmes de piles à combustible respectueux de l’environnement, qui devraient alimenter des machines telles que les véhicules à l’avenir, sont encore rares et coûteux de nos jours. Plusieurs raisons expliquent cela, notamment le processus complexe et onéreux utilisé pour produire les plaques bipolaires, un composant clé des électrolyseurs et des piles à combustible, nécessaires à de nombreux systèmes à hydrogène.
L’Institut Fraunhofer pour les machines-outils et la technologie de formage IWU vient de franchir une étape majeure vers la réduction des coûts et la production de masse des plaques bipolaires en introduisant un système innovant de gaufrage à rouleaux : BPPflexRoll.*
Une efficacité élevée pour les piles à combustible à hydrogène
Les piles à combustible à hydrogène sont très efficaces. Elles utilisent de l’hydrogène et de l’oxygène pour produire de l’électricité, alimentant des machines telles que des véhicules écologiques. Les électrolyseurs inversent ce processus en utilisant de l’énergie électrique pour diviser l’eau en hydrogène et en oxygène. Les deux types de systèmes à hydrogène nécessitent des plaques bipolaires (BPP), qui comprennent deux composants de conversion clés : l’assemblage membrane-électrode (MEA), dans un système de pile à combustible, et la membrane revêtue de catalyseur (CCM), dans un électrolyseur.
Dans une pile à combustible, la structure à double paroi des plaques bipolaires permet à l’oxygène et à l’hydrogène de circuler des deux côtés de la MEA tandis que l’eau refroidit la pile. Le problème est que le processus actuel de production des plaques bipolaires est coûteux, ce qui empêche l’application de la technologie de l’hydrogène et donc, par exemple, l’utilisation généralisée et rentable des véhicules à pile à combustible à hydrogène. Ce potentiel ne peut être libéré que si le coût de la production de masse des composants de base impliqués est réduit.
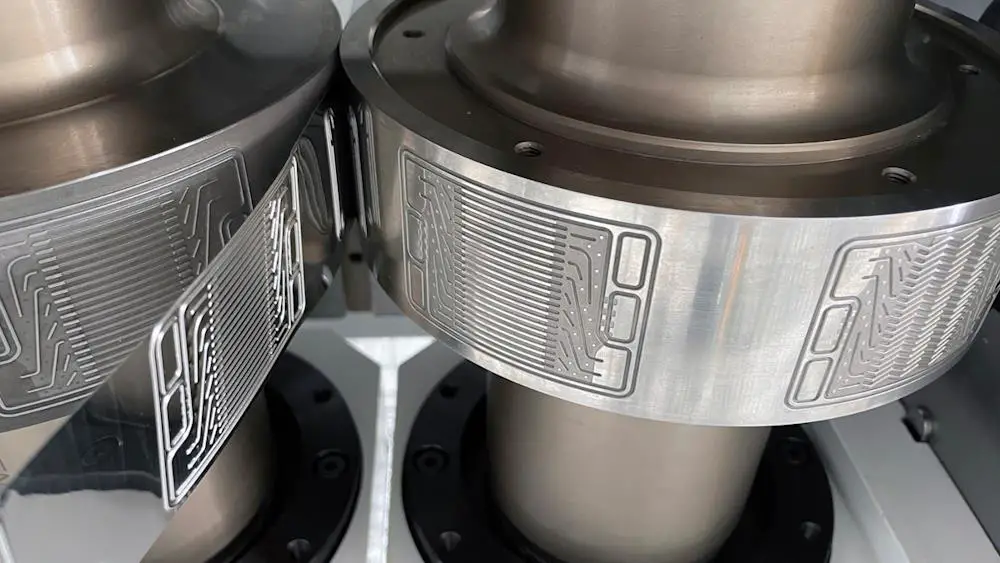
BPPflexRoll : un prototype de système de gaufrage à rouleaux
Les chercheurs de Fraunhofer IWU à Chemnitz, en partenariat avec Profiroll Technologies GmbH, ont développé un prototype de système de gaufrage à rouleaux : BPPflexRoll. La ligne de production est opérationnelle à Fraunhofer IWU. Elle est déjà équipée d’une technologie de contrôle et d’un concept d’exploitation qui s’alignent sur une installation industrielle sur des points clés. Le système se compose de trois stands de rouleaux et nécessite une surface d’installation de 4 500 mm x 3 300 mm.
L’une des raisons pour lesquelles les BPP métalliques sont si coûteuses est qu’elles sont produites par lots discontinus.
« Chaque plaque bipolaire se compose de deux moitiés en acier inoxydable. Les structures pour le flux de gaz et la dissipation de chaleur sont embossées sur les moitiés dans un processus de formage discontinu, puis elles sont assemblées. Notre système de gaufrage à rouleaux a le potentiel de remplacer ces chaînes de processus ou étapes de production discontinues par un processus continu. Sans arrêts ni démarrages, ce processus permettra un volume de production élevé », explique Stefan Polster, responsable du groupe Traitement de la tôle et conception d’outils chez Fraunhofer IWU.
Des avantages significatifs pour la production de plaques bipolaires
« L’un des principaux avantages du gaufrage à rouleaux est la vitesse de processus plus élevée. Jusqu’à 120 demi-plaques BPP peuvent être produites chaque minute », note Robin Kurth, responsable du groupe Machines de formage chez Fraunhofer IWU. Les chercheurs espèrent que ce changement dans les méthodes de production réduira de moitié les coûts de fabrication des BPP.
Dans la nouvelle technologie, la structure de la plaque bipolaire est embossée à l’aide d’une paire de rouleaux, la bande métallique ultra-fine passant en continu entre eux. L’un des rouleaux de formage est défini comme le poinçon, l’autre comme la matrice. Étant donné que les rouleaux utilisés pour former les canaux d’écoulement n’ont qu’un contact linéaire avec la pièce, le formage par étapes peut réduire les forces de processus d’un facteur dix en moyenne par rapport à l’embossage conventionnel. Cela se traduit par une technologie de machine plus petite et moins coûteuse. La flexibilité est un autre avantage du système : le nombre de jeux de rouleaux requis peut être ajusté individuellement, en fonction de la géométrie des plaques bipolaires.
Vers des machines de formage cognitives avec un système de surveillance intégré
Avec le nouveau système pilote, les chercheurs de Fraunhofer IWU font également un pas important vers des machines de formage cognitives, capables de s’auto-surveiller et de se contrôler à l’aide de capteurs et d’algorithmes intelligents. « Contrairement aux systèmes précédents, nous surveillerons à l’avenir la qualité du BPP en temps réel en capturant, consolidant et analysant les paramètres du processus avec des capteurs », déclare Robin Kurth. Les données seront ensuite traitées et rendues utilisables via des solutions cloud.
Les premières plaques bipolaires produites avec l’installation sont déjà testées dans des piles à combustible à l’Institut Fraunhofer pour les systèmes d’énergie solaire ISE à Fribourg.
Avec BPPflexRoll, les chercheurs ouvrent la voie à la production de masse de plaques bipolaires haute efficacité et à faible coût.
* Les chercheurs de Fraunhofer présenteront un composant du système au stand commun de Fraunhofer dans le hall 2, stand B24, au salon Hannover Messe 2024 du 22 au 26 avril.
Légende illustration : Le principal avantage de cette méthode est la vitesse élevée du processus, qui entraîne une augmentation substantielle de la quantité unitaire produite, des économies d’échelle et, en fin de compte, une réduction significative des coûts. Crédit : © Fraunhofer IWU