Des chercheurs du Oak Ridge National Laboratory du ministère de l’énergie ont conçu un nouveau polymère pour lier et renforcer le sable de silice pour la fabrication additive par jet de liant, une méthode d’impression 3D utilisée par les industries pour le prototypage et la production de pièces.
Le polymère imprimable permet de créer des structures de sable aux géométries complexes et à la résistance exceptionnelle, tout en étant soluble dans l’eau.
L’étude, publiée dans Nature Communications, montre un pont de sable imprimé en 3D qui, à 6,5 centimètres, peut supporter 300 fois son propre poids, un exploit comparable à celui de 12 Empire State Buildings assis sur le pont de Brooklyn.
Le procédé d’impression par jet de liant est moins cher et plus rapide que les autres méthodes d’impression 3D utilisées par l’industrie. Il permet de créer des structures 3D à partir de divers matériaux en poudre, offrant ainsi des avantages en termes de coût et d’évolutivité. Le concept s’inspire de l’impression à jet d’encre, mais au lieu d’utiliser de l’encre, la tête de l’imprimante projette un polymère liquide pour lier un matériau en poudre, tel que du sable, construisant ainsi une structure 3D couche par couche. C’est le polymère de liaison qui confère au sable imprimé sa résistance.
L’équipe a utilisé son expertise en matière de polymères pour concevoir un liant en polyéthylèneimine (PEI) qui a permis de doubler la résistance des pièces en sable par rapport aux liants classiques.
Les pièces imprimées par jet de liant sont initialement poreuses lorsqu’elles sont retirées du lit d’impression. Elles peuvent être renforcées en infiltrant la conception avec un matériau supergluant supplémentaire appelé cyanoacrylate qui remplit les espaces. Cette deuxième étape a permis de multiplier par huit la résistance de la première étape, rendant le composite sable-polymère plus solide que tout autre et que tous les matériaux de construction connus, y compris la maçonnerie.
« Peu de polymères sont aptes à servir de liant pour cette application. Nous recherchions des propriétés spécifiques, telles que la solubilité, qui nous donneraient le meilleur résultat. Notre principale découverte a été la structure moléculaire unique de notre liant PEI qui le rend réactif avec le cyanoacrylate pour obtenir une résistance exceptionnelle« , a déclaré Tomonori Saito de l’ORNL, chercheur principal du projet.
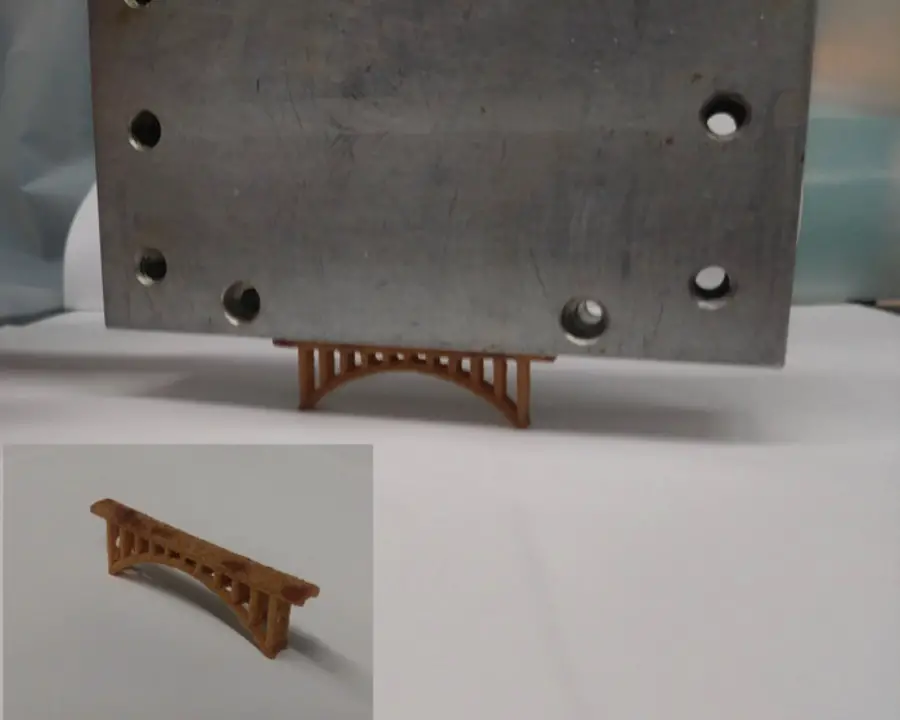
Les pièces formées avec des liants conventionnels sont rendues plus denses grâce à des matériaux d’infiltration, comme la super colle, mais aucun n’a atteint une performance proche de celle du liant PEI. L’impressionnante résistance du liant PEI provient de la façon dont le polymère réagit pour se lier au cyanoacrylate pendant le durcissement.
Une application potentielle du sable super résistant est l’amélioration de l’outillage pour la fabrication de composites.
Le sable de silice est un matériau bon marché et facilement disponible qui suscite un intérêt croissant dans les secteurs de l’automobile et de l’aérospatiale pour la création de pièces composites. Les matériaux légers, tels que la fibre de carbone ou la fibre de verre, sont enroulés autour de noyaux de sable imprimés en 3D, ou « outils », et durcis à la chaleur. Le sable de silice est intéressant pour l’outillage car il ne change pas de dimensions lorsqu’il est chauffé et parce qu’il offre un avantage unique en matière d’outillage lavable. Dans les applications composites, l’utilisation d’un liant soluble dans l’eau pour former des outils en sable est importante car elle permet une simple étape de lavage à l’eau du robinet pour enlever le sable, laissant une forme composite creuse.
« Pour garantir la précision des pièces d’outillage, il faut un matériau qui ne change pas de forme pendant le processus, c’est pourquoi le sable de silice est prometteur. Le défi a été de surmonter la faiblesse structurelle des pièces en sable« , a déclaré Dustin Gilmer, étudiant au Bredesen Center de l’université du Tennessee et auteur principal de l’étude.
Les moules et noyaux actuels de moulage en sable ont un usage industriel limité car les méthodes commerciales, telles que l’outillage de lavage, appliquent une chaleur et une pression qui peuvent provoquer la rupture ou l’échec des pièces en sable dès le premier essai. Des pièces en sable plus résistantes sont nécessaires pour soutenir la fabrication à grande échelle et permettre une production rapide de pièces.
« Notre composite de sable polymère à haute résistance augmente la complexité des pièces qui peuvent être fabriquées avec des méthodes de projection de liant, permettant des géométries plus complexes, et élargit les applications pour la fabrication, l’outillage et la construction« , a déclaré Gilmer.
Le nouveau liant a remporté un prix R&D 100 en 2019 et a été licencié par le partenaire industriel ExOne pour la recherche.
L’article de la revue est publié sous le titre « Additive manufacturing of strong silica sand structures enabled by polyethyleneimine binder. »
Les travaux ont été parrainés par l’Office of Energy Efficiency and Renewable Energy du DOE et ont utilisé des ressources soutenues par l’Office of Science du DOE.
L’UT-Battelle gère l’ORNL pour le compte de l’Office of Science du ministère de l’énergie, le plus grand soutien à la recherche fondamentale en sciences physiques aux États-Unis.
CREDIT : Dustin Gilmer/University of Tennessee, Knoxville