Des chercheurs européens ont récemment réussi à souder au laser deux moitiés d’une section de fuselage de huit mètres de long, fabriquée en fibre de carbone renforcée. Cette réalisation ouvre la voie à la fabrication d’avions de passagers ultra-légers grâce à cette approche innovante.
Un large consortium international, dirigé par Airbus et incluant plusieurs instituts Fraunhofer, a démontré la faisabilité de l’assemblage sans copeaux de structures en thermoplastique renforcé de fibres de carbone (CFRTP) à l’aide d’un laser au dioxyde de carbone.
Le projet «Multifunctional Fuselage Demonstrator» (MFFD), partie intégrante du programme de recherche européen « Clean Sky 2 », a permis de réduire considérablement le poids, les matériaux et le temps nécessaires à la construction d’avions.
La technique de soudage au laser
Les chercheurs de l’Institut Fraunhofer pour la technologie des matériaux et des faisceaux (IWS) à Dresde ont utilisé une source de CO2 pour souder de longues coutures sur des structures composites en fibre thermoplastique, en dehors d’un autoclave. Cette méthode est considérée comme une première mondiale.
«Sur le côté gauche du MFFD, l’approche développée à Fraunhofer IWS a produit la couture longitudinale finale entre les moitiés supérieure et inférieure d’une section de fuselage de huit par quatre mètres, fabriquée en thermoplastiques renforcés de fibres de carbone – à l’échelle réelle,» ont rapporté Maurice Langer et ses collègues.
La longueur d’onde de 10,6 µm du laser CO2 joue un rôle crucial grâce à une absorption optique beaucoup plus élevée que celle des lasers à fibre émettant à 1 µm, couramment utilisés dans le soudage industriel.
Utiliser un laser permet d’éviter les éléments de fixation mécaniques et le doublement de matériau avec des joints rivetés classiques, ce qui allège considérablement la coque en matériau composite thermoplastique par rapport aux sections conventionnelles.
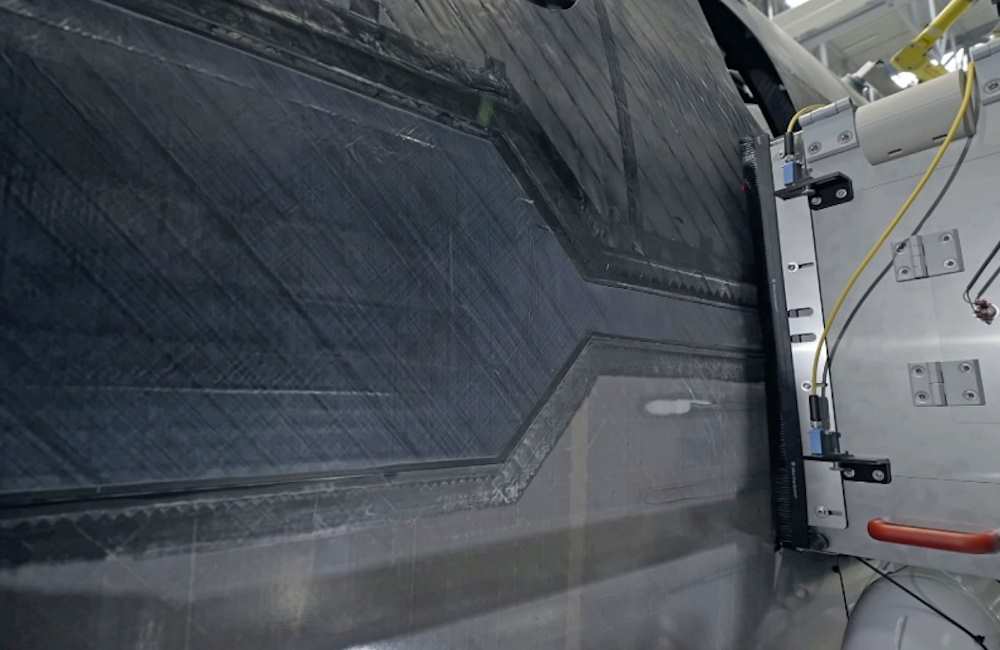
Réduction de l’empreinte écologique
Sur la durée de vie de l’avion, le poids significativement réduit diminue les besoins énergétiques globaux, la consommation de carburant et les émissions associées.
«Avec le processus CONTIjoin développé à Fraunhofer IWS, nous avons franchi une étape économique et écologique importante pour le développement futur des avions et des applications connexes,» a déclaré Maurice Langer.
Un des éléments clés du projet consistait à assembler les coques supérieure et inférieure du fuselage de manière progressive, en plaçant plusieurs bandes de laminé les unes sur les autres, positionnées automatiquement en une géométrie en escalier sur les surfaces des demi-coques.
«Les joints de recouvrement résultants rétablissent le flux de force initialement interrompu du matériau composite entre les demi-coques et forment un joint fiable pour le transfert de charge,» a expliqué l’équipe de l’IWS.
Module ESL2-100
Un autre développement clé est le module «ESL2-100» de l’IWS, développé en interne à Dresde. Selon Peter Rauscher, responsable du groupe de traitement laser à grande vitesse, ce module permet d’interpréter une grande variété de signaux de capteurs, permettant ainsi la mise en œuvre d’algorithmes de contrôle correspondants.
«Cela offre la possibilité de surveiller et de contrôler de manière adaptative le processus de soudage en temps réel, ce qui ne serait pas possible avec l’électronique de contrôle conventionnelle,» a déclaré Peter Rauscher.
Les plans futurs visent à faire progresser le niveau de maturité technologique (TRL) de l’approche, en vue de sa qualification pour l’industrie aéronautique et au-delà.
«La technologie CONTIjoin développée est attrayante pour la construction aéronautique et d’autres industries,» a souligné Maurice Langer. «En plus de l’aviation, la solution pourrait également être intéressante pour des applications dans la construction navale, la construction de camions et de remorques, ainsi que dans le transport ferroviaire ou le développement de turbines éoliennes modernes.»
Légende illustration: Un segment de fuselage en matériaux thermoplastiques CFRP a été fabriqué pour la première fois en taille réelle, dans le cadre du projet plus large Clean Sky 2. L’objectif est de permettre une évaluation bien fondée de la faisabilité ainsi que des avantages et inconvénients écologiques et économiques. La coque du fuselage en matériau composite thermoplastique pèse nettement moins que les sections conventionnelles. Photo : Clean Aviation.