Un événement majeur s’est produit en Angleterre dans l’industrie de la construction, avec l’introduction du premier élément d’infrastructure en béton imprimé en 3D dans un projet national. Cette réalisation marque un tournant significatif pour l’industrie et pourrait changer la façon dont nous construisons l’avenir.
Les chercheurs de l’université de Cambridge, en collaboration avec des acteurs industriels, ont aidé à développer la première infrastructure en béton imprimée en 3D pour un projet National Highways. Il s’agit d’un type de mur de soutènement appelé « headwall« , installé sur l’A30 en Cornouailles.
Cette structure novatrice fournit des informations en temps réel grâce à des capteurs conçus à Cambridge et intégrés à sa structure. Ces capteurs offrent des mesures à jour, incluant la température, la tension et la pression. Cette réplique numérique du mur pourrait aider à détecter et à corriger les défauts avant qu’ils ne surviennent.
Un mur de soutènement imprimé en 3D, une première
Cette paroi de soutènement, appelée tête de mur, a été imprimée en 3D. Contrairement aux éléments standards préfabriqués en béton avec coffrage et armatures métalliques, ce mur incurvé creux a été réalisé sans coffrage ni acier. Sa solidité repose sur sa géométrie.
Le mur de deux mètres de haut sur trois mètres et demi de large n’a nécessité qu’une heure d’impression dans les locaux de l’entreprise d’ingénierie avancée Versarien, à l’aide d’un bras robotisé. Réalisé par impression 3D, ce mur permet des économies importantes en termes de coûts, de matériaux et d’émissions carbone.
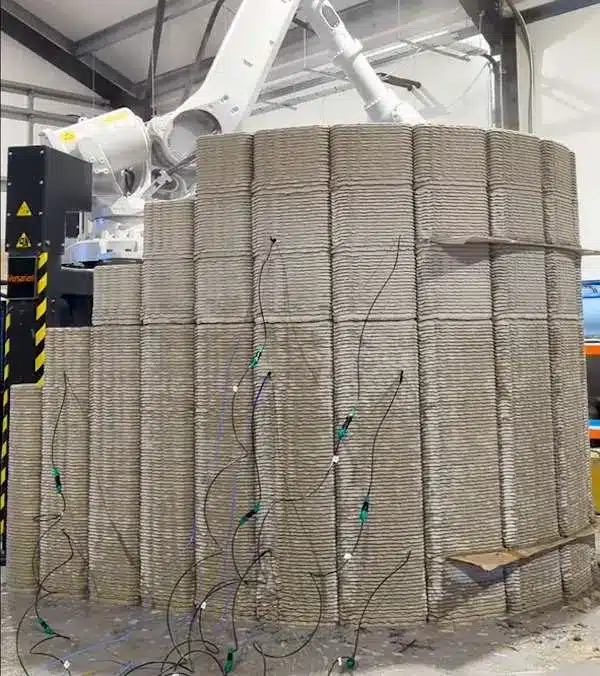
Des capteurs intégrés pour un jumeau numérique
Depuis six ans, le Pr Abir Al-Tabbaa et son équipe au Département d’ingénierie de Cambridge développent de nouvelles technologies de capteurs et testent l’efficacité de capteurs commerciaux. Le but : collecter des données de meilleure qualité sur les infrastructures. Ils ont aussi mis au point des bétons auto-réparants « intelligents« .
Pour ce projet, ils ont fourni des capteurs de température pour contrôler l’impression 3D. Les variations ont été surveillées couche par couche pour détecter des points chauds ou anomalies thermiques. Ces données seront corrélées avec l’imagerie thermique du mur imprimé en 3D pour comprendre son comportement thermique.
« Un ciment à prise ultra-rapide génère énormément de chaleur pendant l’impression 3D, explique le Pr Al-Tabbaa. Nous avons intégré nos capteurs dans le mur pour mesurer la température pendant la construction, et maintenant nous recevons des données alors que le mur est sur site. »
En plus de la température, les capteurs mesurent l’humidité relative, la pression, la déformation, la résistivité électrique et le potentiel électrochimique. Ces mesures apportent des informations précieuses sur la fiabilité, la robustesse, la précision et la longévité des capteurs.
Un système LiDAR a également scanné le mur pendant l’impression pour créer un nuage de points 3D et générer un jumeau numérique.
« Rendre ce mur digital signifie qu’il peut parler de lui-même, analyse le Pr Al-Tabbaa. Nos capteurs nous permettront de mieux comprendre ces structures imprimées en 3D et d’accélérer leur acceptation dans l’industrie. »
Des perspectives intéressantes
L’équipe de Cambridge a développé des capteurs piézoélectriques qui mesurent la réponse électromécanique. Ils détectent les changements dans le temps pour identifier d’éventuels dommages. Ces capteurs intelligents montrent le durcissement du mortier imprimé en 3D tout en surveillant l’état de santé de la structure.
Huit de ces capteurs piézoélectriques ont été intégrés dans les différentes couches du mur pendant l’impression 3D. Ils captent la présence de charge et de déformation pendant la construction et en service.
L’équipe pluridisciplinaire de Cambridge, rassemblant des spécialistes en matériaux intelligents, automatisation, robotique, science des données, a aussi développé un système d’acquisition de données sans fil dédié. Il permet de collecter à distance les réponses électromécaniques multifréquences des capteurs embarqués.
« Ce projet servira de laboratoire vivant, générant des données précieuses pendant toute sa durée de vie, se réjouit le Pr Al-Tabbaa. Les données des capteurs et le jumeau numérique aideront les professionnels des infrastructures à mieux appréhender l’impression 3D, pour l’utiliser et l’adapter afin d’imprimer des matériaux à base de ciment plus grands et complexes pour le réseau routier stratégique. »
En synthèse
L’impression 3D ouvre de nouvelles perspectives dans la construction d’infrastructures. Les chercheurs de Cambridge font œuvre de pionniers avec ce mur de soutènement doté de capteurs intégrés. Il constitue un jumeau numérique qui permet un suivi en temps réel de l’ouvrage. Cette innovation devrait accélérer l’adoption de l’impression 3D, plus économique et écologique, dans les projets du BTP. Les données générées par les capteurs offriront aussi une meilleure connaissance du comportement des structures imprimées en 3D.
Pour une meilleure compréhension
Qu’est-ce qu’une tête de mur ?
Une tête de mur est un élément de soutènement qui retient la poussée des terres.
Quels sont les avantages de l’impression 3D pour ce type de structure ?
L’impression 3D permet de s’affranchir des contraintes du béton préfabriqué standard. On peut créer des formes complexes (ici incurvées), sans coffrage ni armatures métalliques.
Comment les capteurs intégrés créent-ils un jumeau numérique ?
Les capteurs mesurent en permanence différents paramètres (température, humidité, déformation…). Ces données en temps réel permettent de surveiller précisément l’état de l’ouvrage.
En quoi ce projet est-il novateur ?
C’est la première utilisation de l’impression 3D pour une infrastructure routière majeure au Royaume-Uni. Les capteurs intégrés ouvrent aussi la voie à une maintenance prédictive des ouvrages.
Les travaux de l’équipe de Cambridge s’inscrivent dans le cadre du programme Resilient Materials for Life et de l’initiative Digital Roads of the Future. La recherche est soutenue en partie par l’Engineering and Physical Sciences Research Council (EPSRC), qui fait partie du UK Research and Innovation (UKRI), et par l’Union européenne.
Photos :- Credit Cambridge