Yasmin Ahmed Salem
Une méthode en une seule étape permet d’économiser de l’énergie grâce à l’extrusion du nickel et de réduire les émissions de CO2 pour les batteries et l’acier inoxydable.
Points forts |
---|
Une demande en nickel difficile à satisfaire : la demande en nickel devrait doubler, alors que la production conventionnelle de nickel émet environ 20 tonnes de CO2 par tonne de nickel. Un nouveau procédé durable pour la production de nickel : des chercheurs ont trouvé un moyen d’extraire le nickel de minerais de faible teneur en utilisant du plasma d’hydrogène à la place du carbone. Ce procédé en une seule étape ne produit pas de CO2 et permet d’économiser de l’énergie et du temps. Possibilité d’augmentation de la production : pour augmenter la production, il est nécessaire de mettre en place des arcs courts à courant élevé, d’intégrer un dispositif de brassage électromagnétique externe sous le four ou d’utiliser l’injection de gaz, en veillant à ce que la masse fondue non réduite atteigne en continu l’interface de réaction. |
Pour lutter contre le changement climatique et parvenir à une industrie climatiquement neutre, les émissions de carbone doivent être réduites de manière drastique. Un élément clé de cette transition est le remplacement des vecteurs énergétiques à base de carbone par l’électricité, en particulier dans les transports et les applications industrielles. Toutefois, cette transition dépend fortement du nickel, un matériau essentiel utilisé dans les batteries et l’acier inoxydable. D’ici 2040, la demande de nickel devrait doubler en raison de l’électrification croissante des infrastructures et des systèmes de transport. Or, la production d’une tonne de nickel émet actuellement environ 20 tonnes de CO2, ce qui soulève des inquiétudes quant au transfert de la charge environnementale du transport vers la métallurgie.
Des chercheurs de l’Institut Max Planck pour les matériaux durables ont mis au point une méthode d’extraction du nickel sans carbone et économe en énergie. Leur approche permet également d’utiliser des minerais de nickel à faible teneur, qui ont été négligés en raison de la complexité des processus d’extraction conventionnels. L’équipe de Max Planck a publié ses résultats dans la revue Nature.

Une seule étape vers le nickel vert
«://www.enerzine.com/rubisco-lenzyme-qui-capture-100-gigatonnes-de-carbone-par-an-devoile-ses-secrets/155325-2025-01″ data-wpil-monitor-id= »6581″>carbone. Cette approche permet non seulement de réduire les émissions de CO2 de 84 %, mais aussi d’améliorer l’efficacité énergétique de 18 % lorsqu’elle est alimentée par de l’électricité renouvelable et de l’hydrogène vert.
Traditionnellement, l’industrie s’appuie sur des minerais de haute qualité, car l’extraction du nickel à partir de minerais de moindre qualité est beaucoup plus complexe en raison de leur composition chimique complexe. Contrairement au fer, qui peut être réduit en une seule étape en éliminant l’oxygène, le nickel présent dans les minerais de faible qualité est chimiquement lié à des silicates de magnésium ou des oxydes de fer complexes. L’extraction conventionnelle implique plusieurs étapes telles que la calcination, la fusion, la réduction et le raffinage, qui sont très énergivores et ont une empreinte carbone importante. Une avancée majeure de cette méthode réside dans sa capacité à traiter des minerais de nickel de faible teneur (qui représentent 60 % des réserves totales de nickel) dans un seul four à réacteur, où la fusion, la réduction et le raffinage se produisent simultanément, produisant directement un alliage de ferronickel raffiné.
« En utilisant le plasma d’hydrogène et en contrôlant les processus thermodynamiques à l’intérieur du four à arc électrique, nous sommes en mesure de décomposer la structure complexe des minéraux présents dans les minerais de nickel de faible teneur en espèces ioniques plus simples, même sans utiliser de catalyseurs », ajoute Isnaldi Souza Filho, chef de groupe à l’Institut Max Planck pour les matériaux durables.
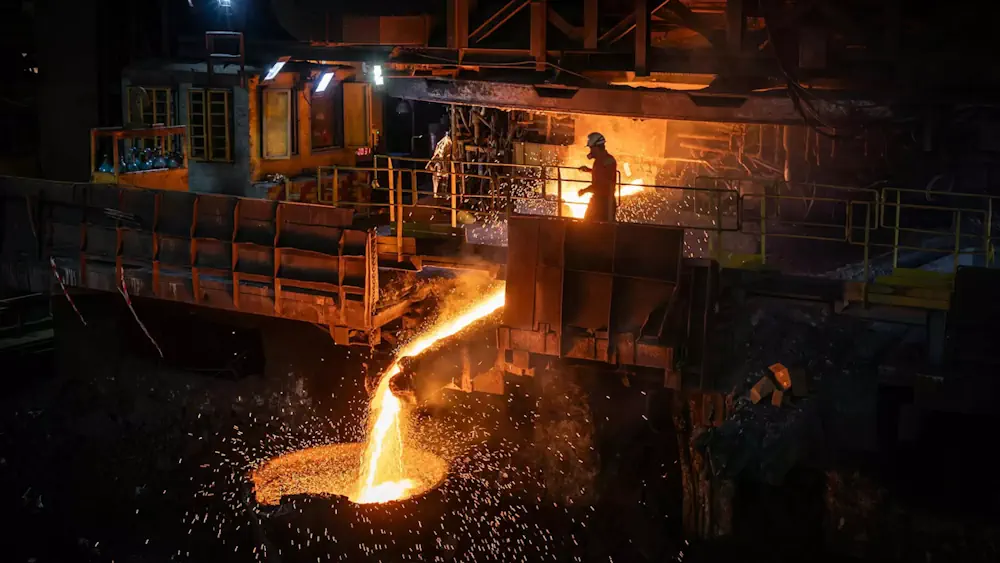
Vers une application industrielle
Cette méthode permet non seulement de réduire les émissions et la consommation d’énergie, mais aussi d’élargir le spectre des minerais de nickel utilisables, rendant l’extraction plus rentable et plus durable. La prochaine étape pour l’équipe Max Planck consiste à adapter le processus à des applications industrielles.
« La réduction des minerais de nickel en espèces ioniques plus simples ne se produit qu’à l’interface de réaction, et non dans l’ensemble de la masse fondue », précise Ubaid Manzoor. « Dans un système à plus grande échelle, il est essentiel de s’assurer que la masse fondue non réduite atteigne en permanence l’interface de réaction. » Cela peut être réalisé en mettant en place des arcs courts à courant élevé, en intégrant un dispositif de brassage électromagnétique externe sous le four ou en recourant à l’injection de gaz. Il s’agit là de techniques industrielles bien établies, ce qui rend leur intégration dans les processus existants tout à fait réalisable.
La filière de production de nickel vert ouvre la voie à une électrification plus durable du secteur des transports. L’alliage de nickel réduit peut être utilisé directement dans la production d’acier inoxydable et, après un raffinage supplémentaire, comme matériau pour les électrodes de batteries. De plus, les scories produites lors du processus de réduction peuvent constituer une ressource précieuse pour l’industrie de la construction, notamment pour la production de briques et de ciment. Le même processus peut également être appliqué au cobalt, qui est utilisé dans les véhicules électriques et les systèmes de stockage d’énergie.
Article : « Sustainable nickel enabled by hydrogen-based reduction » – Auteurs : U. Manzoor, L. Mujica Roncery, D. Raabe, I.R. Souza Filho – DOI : 10.1038/s41586-025-08901-7
Source : Max Planck