Des chercheurs américains ont mis au point une méthode novatrice de fabrication utilisant la technologie laser. Cette approche permet de créer des dispositifs complexes intégrant divers matériaux, tels que les plastiques, les métaux et les semi-conducteurs, le tout à l’aide d’une seule machine. Les applications potentielles de cette technologie sont nombreuses et variées, allant des capteurs environnementaux aux dispositifs médicaux portables.
La recherche, publiée dans la revue Nature Communications, présente un procédé inédit combinant l’impression 3D et le traitement laser. Cette méthode, baptisée « Freeform Multi-material Assembly Process » (Processus d’assemblage multi-matériaux Freeform), permet la fabrication de capteurs multicouches, de circuits imprimés et même de textiles intégrant des composants électroniques.
Selon l’annonce de l’Université du Missouri, la machine est capable d’imprimer des capteurs directement intégrés dans une structure. Les dispositifs ainsi créés peuvent mesurer diverses conditions environnementales, notamment la température et la pression. Les applications potentielles sont vastes : des objets d’apparence naturelle, comme un rocher ou un coquillage, pourraient être utilisés pour mesurer les mouvements de l’eau océanique. Dans le domaine grand public, des dispositifs portables permettant de surveiller la tension artérielle et d’autres signes vitaux sont envisageables.
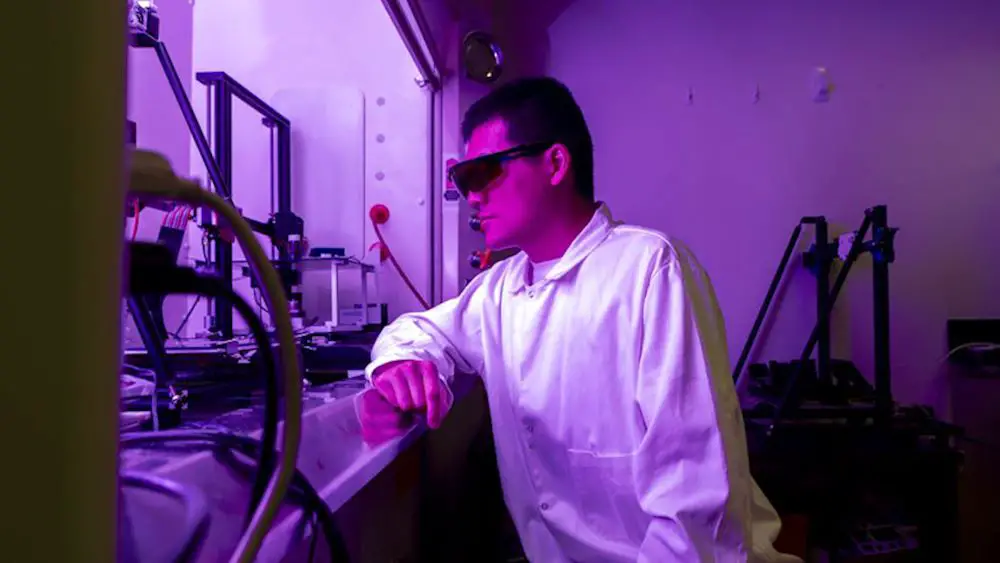
Une innovation prometteuse pour la recherche et l’industrie
Bujingda Zheng, doctorant en génie mécanique à l’Université du Missouri et auteur principal de l’étude, exprime son enthousiasme : «C’est la première fois qu’un tel procédé est utilisé, ouvrant ainsi de nouvelles possibilités. Je suis ravi de la conception. J’ai toujours voulu faire quelque chose que personne n’avait jamais fait auparavant, et j’y parviens ici.»
L’un des principaux avantages du Freeform Multi-material Assembly réside dans la possibilité pour les innovateurs de se concentrer sur la conception de nouveaux produits sans se soucier de leur prototypage. Jian «Javen» Lin, professeur associé de génie mécanique et aérospatial à l’Université du Missouri, souligne : «Cela ouvre la voie à des marchés entièrement nouveaux. Les impacts seront considérables sur les capteurs portables, les robots personnalisables, les dispositifs médicaux et bien d’autres domaines.»
Une technologie inspirée par la nature
Zheng explique le concept sous-jacent : «Tout dans la nature est composé de matériaux structurels et fonctionnels. Par exemple, les anguilles électriques possèdent des os et des muscles qui leur permettent de se déplacer. Elles disposent également de cellules spécialisées capables de décharger jusqu’à 500 volts pour dissuader les prédateurs.»
La méthode développée par l’équipe utilise des techniques spéciales pour résoudre les défis liés à la fabrication de tels dispositifs complexes. Les chercheurs ont construit une machine équipée de trois buses différentes : l’une ajoute un matériau semblable à de l’encre, une autre utilise un laser pour sculpter des formes et des matériaux, et la troisième ajoute des matériaux fonctionnels supplémentaires pour améliorer les capacités du produit.
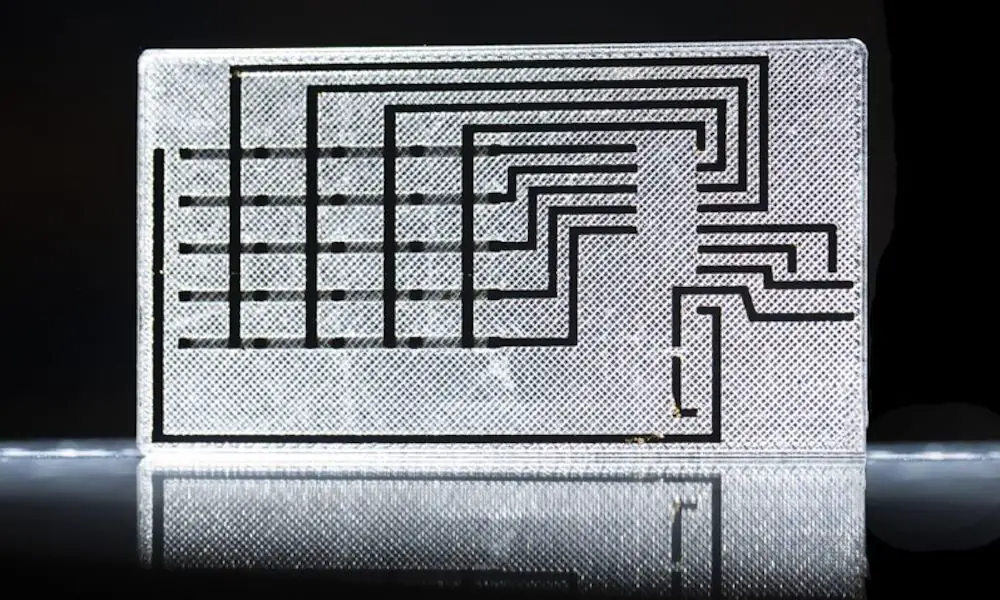
Un processus de fabrication en plusieurs étapes
Le processus débute par la création d’une structure de base à l’aide d’un filament d’impression 3D standard, tel que le polycarbonate, un thermoplastique transparent. Ensuite, le laser entre en action pour convertir certaines parties en un matériau spécial appelé graphène induit par laser, le plaçant exactement où il est nécessaire. Enfin, d’autres matériaux sont ajoutés pour améliorer les capacités fonctionnelles du produit final.
Ce travail est financé par le programme Advanced Manufacturing de la Fondation nationale des sciences des États-Unis (NSF), tandis que le programme I-Corps de la NSF fournit des fonds pour explorer les possibilités de commercialisation.
Le professeur Lin précise : «Le programme I-Corps nous aide à identifier les intérêts et les besoins du marché. Actuellement, nous pensons que cela intéresserait d’autres chercheurs, mais nous croyons qu’à terme, les entreprises en bénéficieront. Cela réduira le temps de fabrication des prototypes de dispositifs en permettant aux entreprises de les réaliser en interne. Cette technologie, disponible uniquement à l’Université du Missouri, montre un grand potentiel pour transformer la façon dont les produits sont fabriqués et manufacturés.»
L’émergence de cette technologie novatrice ouvre de nouvelles perspectives dans le domaine de la fabrication additive et de la conception de produits complexes.
Légende illustration : Un laser violet grave les matériaux Des chercheurs de l’université du Missouri ont construit une machine qui combine des éléments de l’impression 3D traditionnelle avec la technologie laser pour développer des produits multimatériaux et multifonctionnels. Crédit : photos Sam O’Keefe