L’innovation dans le domaine des matériaux durables suscite un intérêt croissant, notamment en raison de la nécessité de réduire l’empreinte carbone des industries. Une entreprise californienne, Mango Materials, a développé une technologie innovante qui pourrait transformer la manière dont nous produisons et utilisons les plastiques.
Mango Materials utilise des bactéries capables de consommer du méthane pour fabriquer des polymères pouvant remplacer les plastiques traditionnels, souvent très polluants. Le méthane, un gaz à effet de serre puissant, est naturellement produit dans plusieurs industries essentielles telles que l’agriculture et le traitement des eaux usées. L’idée est de capter ce gaz avant qu’il ne soit libéré dans l’atmosphère et de le transformer en quelque chose d’utile.
La société a mis au point un procédé utilisant des micro-organismes spécifiques qui convertissent le méthane en polyhydroxyalcanoate (PHA), un polymère biodégradable. Ce PHA peut être transformé en granulés de polyester biodégradables à 100 %, utilisés pour fabriquer des biens durables, des tissus et des films flexibles. Ces matériaux à base de PHA se décomposent beaucoup plus rapidement que les plastiques traditionnels, revenant au méthane et au dioxyde de carbone en quelques semaines ou mois, selon l’épaisseur du produit.
Processus de production et collaboration avec Berkeley Lab
Allison Pieja, cofondatrice et directrice technique de Mango Materials, a déclaré : « Nous travaillons sur un processus à bilan carbone négatif. Nos analyses montrent qu’il devrait être négatif en termes de carbone lorsqu’il fonctionnera à pleine échelle. »
La société a récemment achevé la construction d’une installation de production de PHA dans une station d’épuration à Vacaville, en Californie. Le méthane produit par les microbes nettoyant l’eau publique est capté et acheminé directement dans des bioréacteurs contenant les bactéries consommatrices de méthane. Mango Materials produit déjà suffisamment de PHA pour fabriquer des produits de démonstration, comme un porte-savon disponible à la vente et deux prototypes de produits de mode : une paire de baskets net-zéro d’Allbirds et des lunettes de soleil durables du célèbre designer Stella McCartney.
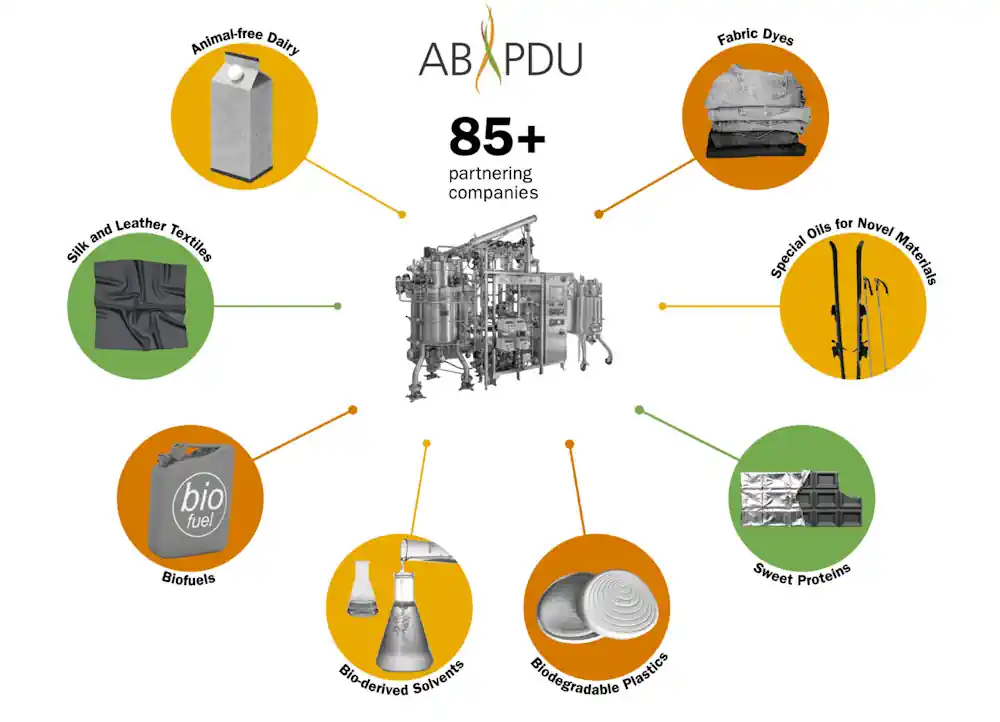
Optimisation et mise à l’échelle de la production
La transition de Mango Materials d’un concept en laboratoire à un processus commercial efficace a nécessité du temps. Les scientifiques du Unité de développement des procédés avancés pour les biocarburants et les bioproduits (ABPDU) du Berkeley Lab ont aidé à affiner ce processus. Après la fondation de l’entreprise en 2012, l’équipe de Mango a passé des années à optimiser à la fois la culture bactérienne – qui produit naturellement du PHA et n’est pas génétiquement modifiée – et les conditions de croissance favorisant une production élevée de PHA.
Pour maximiser la quantité et la pureté du PHA récupéré, Mango a collaboré avec une équipe de l’ABPDU dirigée par Ning Sun. Ensemble, ils ont testé des équipements pertinents à l’échelle industrielle pour déterminer ce qui fonctionnait avant d’investir dans leurs propres systèmes pilotes.
Purification et extraction du PHA
Les bactéries transforment le méthane en chaînes de PHA pour stocker de l’énergie, similaire à la manière dont les plantes stockent de l’énergie dans des amidons. Les molécules s’accumulent à l’intérieur des cellules. En travaillant côte à côte, l’équipe de Sun et les scientifiques de Mango ont testé des équipements et affiné les processus pour extraire les cellules du « bouillon » à l’intérieur du bioréacteur, ouvrir les parois et membranes cellulaires bactériennes, puis séparer le PHA des autres produits cellulaires.
Ning Sun a précisé : « Nous avons reçu du bouillon de l’équipe d’Allison à différentes échelles, la plus grande étant de plusieurs centaines de litres. Nous avons essayé différentes opérations de récupération pour optimiser les conditions et augmenter le rendement de récupération ainsi que la pureté du produit final. »
Impact et perspectives
À la fin du projet, ralenti par la pandémie de COVID-19, la collaboration avait mis au point un processus répondant aux objectifs de rendement élevé. Pieja et ses collègues savaient désormais quel équipement de traitement en aval investir pour leur propre installation de production.
« Ce travail a été vraiment essentiel pour nous en ayant accès à une installation de traitement en aval et à des personnes qui savent comment l’utiliser », a ajouté Allison Pieja. « Nous avons pu évaluer en profondeur plusieurs technologies différentes pour comprendre comment notre plateforme se comportait en elles. Nous avons maintenant un processus dont nous sommes convaincus qu’il sera rentable. »
En parallèle, l’équipe de l’ABPDU a acquis une expertise supplémentaire dans l’extraction de biopolymères intracellulaires. À ce jour, l’ABPDU a collaboré avec 85 partenaires industriels allant des start-ups aux entreprises de biotechnologie établies, ainsi qu’avec 20 laboratoires nationaux, centres de recherche et universités pour aider à la mise à l’échelle ou au lancement de produits innovants basés sur la biologie.
Asun Oka, ingénieur de procédé senior de l’équipe de Sun, a conclu : « Nous avons certainement beaucoup appris de cette collaboration. L’équipe a pu mettre à l’échelle un processus de laboratoire et tester différentes configurations d’équipements de récupération de produits, ce qui sera applicable à la récupération de biopolymères similaires. »
L’installation de lancement de Mango Materials utilise les émissions de gaz méthane comme matière première pour fabriquer des matériaux biodégradables. Crédit : Mango Materials